This article is part of the Carbon Footprint series:
- Rapid introduction to the CRE bidding mechanism
- Introduction to Simplified Carbon Footprint: calculation
- LCA and optimized carbon values: method 2 & documentary process
- Impact of the manufacturing country and process: what are the optimization targets?
- Low carbon supply: The Norwegian question
- Low carbon modules: what are the promising alternatives
- Is Polysilicon FBR a solution for the French market?
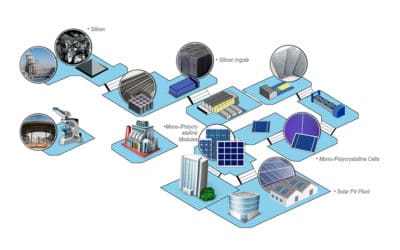
The norwegian upstream insufficient supply is hardly beatable from a carbon footprint point of view:
Crystalline PV modules manufacturers quickly realized that producing modules based on a Norwegian upstream supply is the simplest and quickest solution to deploy an offer with a favorable carbon footprint for CREs AO (call for tenders).
Supported by a favorable electric mix, the Norwegian upstream industry was the first to carry out LCAs on the advice of French developers, who quickly identified the optimization paths (less energy-intensive process such as metallurgical purification, or the use of recycled poly-silicon in the ingots) and above all an electric mix with carbon content among the lowest on the planet.
Thus, for the CRE3 period, almost all the winners were awarded thanks, partly, to the modules produced from Polysilicon and ingots (sometimes even Wafers) made in Norway. The final values obtained by the module manufacturers are very competitive in the range of 400 kgCO2eq / kWp. The successive improvements brought these values to levels that were sometimes even below 350 kgCO2eq / kWp.
Tier-1 players to enter the game
When the AOs (call for tenders) were launched, the world leading manufacturers showed a limited interest in performing Life Cycle Assessment and a specific carbon footprint certification.
Since then, the awarded volumes have significantly increased and the dynamics of the AO have been perpetuated. Thus, Tier 1 manufacturers are beginning to take a close interest in French Tenders and the related carbon footprint challenge.
Unfortunately, many have chosen the easy way by opting for a Norwegian upstream supply, thus underestimating the consequences of their future dependence on this insufficient supply.
That said, one must understand that by investing in their competitiveness, which intends, above all, to lowering the production costs, while increasing the efficiency of their modules, these “top manufacturers” with high production capacity indirectly invest in reducing their carbon footprint. As a matter of fact, less material and less energy consumed for a more powerful module results beyond the lowering of production costs per watt peak, to considerably reduce environmental impact.
Yet to be identified: the most relevant processes and a specially-dedicated “low carbon” supply chain that could be a pertinent alternative to Norway.
Recycling and reduction of material losses
In recent years, the industry has been wondering how to minimize the costly material losses that occur upstream of the value chain during the sawing of ingots and wafers. At the end of these two stages, more than 60% of polysilicon is lost during the manufacturing of a polycrystalline wafer and 75% for a monocrystalline wafer.
Today, some ingots and wafer manufacturers have implemented recycling processes at their production sites, which, in addition to saving money, can reduce their carbon impact. They reincorporate the losses as material during the manufacturing steps of new ingots, and this on a large scale.
Another representative example is the sawing of wafers with diamond wire (DWS), which reduces the losses while reducing the energy consumption necessary for the process. Today this slicing method is widely adopted by the leaders of wafers manufacturing.
Increases in module power leads to carbon footprint optimization
Innovation in manufacturing processes as well as cells and modules architecture not only participates in maximizing modules power output , it also contributes heavily in reducing the carbon footprint value per kilowatt-peak.
PERC cells, N-Type, half-cell modules, shingled cells, bifacial etc … These products are already part of the mass production product range offered by the Tier-1 manufacturers, which are the pillars of the photovoltaic sector’s R&D.
Towards a competitive carbon footprint, even in the countries with unfavorable electricity mix.
Even by using polysilicon from Korea (a country with a large polysilicon industry and a decent carbon content of its electrical mix), and combining it with all the previously described improvements, we cannot be as good as the Norwegian scenario, in terms of carbon impact.
As laureates are committed to installing the modules they have previously registered during their project application, the problem of shortage will sooner or later weight on the supply of modules for the French tenders and is likely to intensify.
It will thus be necessary to seek other industrially realistic solutions to cope with this challenge. What we will see in a forthcoming chapter.
LCA : Life Cycle Analysis