IMPACT CARBONE & AO CRE – Impact des pays de fabrication et process : quelles sont les cibles d’optimisation ?
Cet article fait partie de la série Bilan carbone :
- Rapide introduction aux mécanismes d'appels d'offres
- Introduction à l'Évaluation Carbone Simplifiée : calcul
- ACV et valeurs carbone optimisées : présentation de la méthode 2 et du processus documentaire
- Impact des pays de fabrication et process : quelles sont les cibles d'optimisation ?
- Supply bas-carbone : la question norvégienne
- Modules low-carbone : quelles sont les alternatives prometteuses ?
- Le Polysilicium FBR une solution pour le marché Français ?
Analyse de l'impact carbone par étape
Avant de se lancer dans la réalisation d’Analyse de Cycle de Vie, il est utile d’analyser le poids de l’impact carbone de chaque étape et composant. Si on regarde la figure 1 ci-après, on se rend rapidement compte que la purification du Polysilicium et la découpe des Wafers représentent plus de la moitié de la valeur finale que ce soit pour le polycristallin ou le monocristallin (en utilisant les valeurs GWP « World » standard du cahier des charges). A noter aussi, l’étape des lingots qui est beaucoup plus impactante pour la technologie mono.
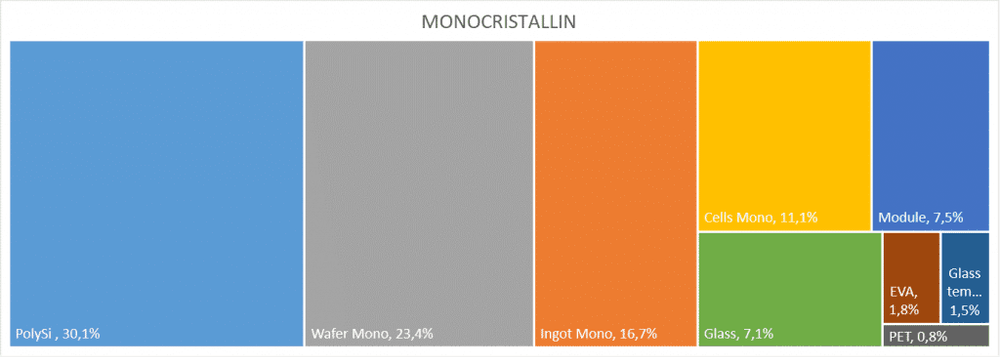
Comme vu précédemment, on peut jouer sur deux critères pour optimiser la valeur finale : le site de fabrication/provenance et la réalisation d’un ACV qui peut mettre en valeur un process économe en énergie. Attention cependant, la réalisation d’ACV ne permet pas toujours de réaliser une optimisation de l’impact carbone, parfois le résultat obtenu n’est pas significativement meilleur si ce n’est moins bon que les valeurs standards. On peut citer par exemple les cellules PERC qui nécessitent plus d’énergie que les cellules standard dans leur fabrication.
Importance de l'origine de production
La première façon de réduire l’impact carbone est d’optimiser l’origine de son supply. Les fabricants de cellules et de modules l’ont bien compris et dès CRE3 ils se sont tournés vers les fournisseurs norvégiens qui produisent polysilicium et/ou lingots en utilisant un mix électrique favorable composé majoritairement d’énergie hydraulique. Ces fournisseurs ont très vite réalisé des ACV sur la partie Polysilicium étant donné que le coefficient standard GWP Norvège pour cette étape ne figure pas dans le tableau du cahier des charge (si méthode 1 obligation d’utiliser le coefficient « World » pénalisant). Ci-dessous quelques valeurs représentatives :
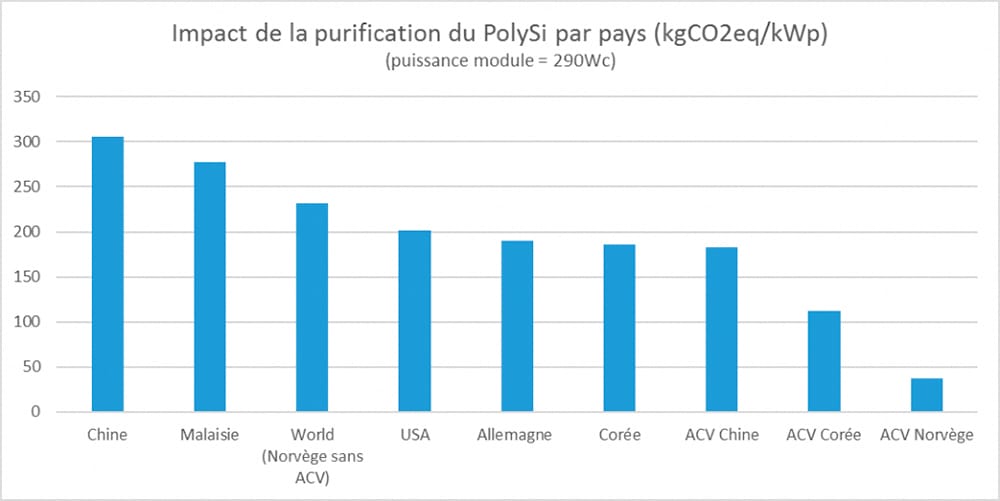
La filière norvégienne a donc pu s’appuyer sur les AO CRE français pour se relancer en redémarrant des usines*. Cependant, leur capacité de production apparaisse souvent insuffisante pour répondre à la demande. Nous aborderons ce sujet dans le chapitre 5.
Optimisation par le process de fabrication
Hormis le pays de fabrication, des économies « carbone » importantes sont réalisables en identifiant et en réalisant des ACV chez les industriels utilisant des process innovants qui nécessitent moins d’énergie et de matières premières. Ces innovations ou optimisations sont industrialisées essentiellement par intérêt économique mais participe en même temps à la diminution de l’impact carbone de la filière PV.
Attardons-nous sur quelques-uns de ces process qui font parler d’eux dans l’industrie PV :
Le Diamond Wire Sawing pour la découpe des wafers
Le sciage au fil diamant (DWS : Diamond Wafer Sawing) permet de réduire le temps de coupe et de produire plus de wafers qu’un sciage classique au fil slurry. Il est aujourd’hui largement utilisé pour le monocristallin mais encore très peu industrialisé pour le polycristallin. Il permet une réduction carbone importante de cette étape : environ 80% par rapport au sciage classique pour le monocristallin et 60% pour le polycristallin (voir Fig. 3).
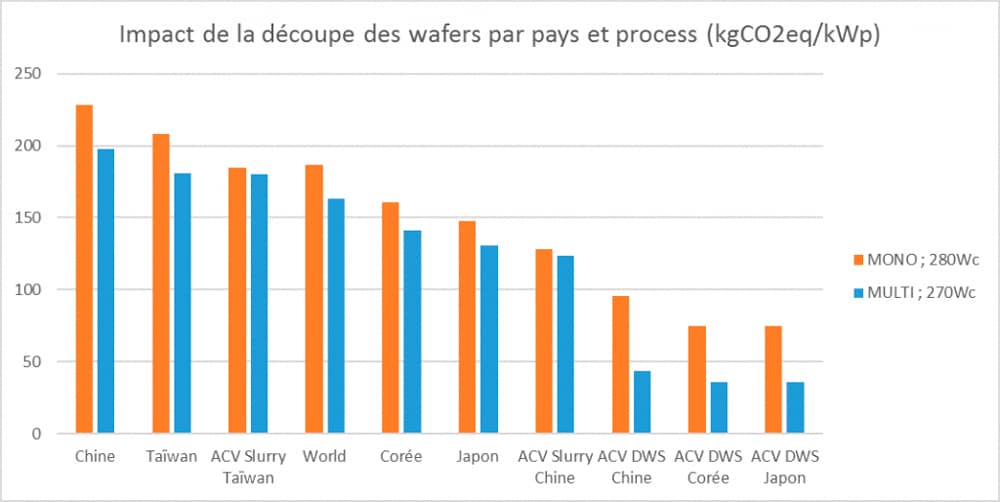
L’utilisation de Polysilicium recyclé dans les lingots
Le recyclage des déchets de coupe des lingots et wafers est assez répandu dans l’industrie PV pour des raisons économiques. Après recyclage, ce polysilicium pour être réutilisé pour couler de nouveaux lingots. Cependant, le polysilicium recyclé n’est pas d’une aussi grande pureté que celui d’origine, il convient donc de l’utiliser dans certaines proportions. Communément, on se limite à 70% pour un lingot monocristallin et à 40-50% pour un polycristallin. Ceci permet de réduire encore plus l’impact final car le polysilicium recyclé ayant fait l’objet d’un ACV aura une empreinte carbone minime.
Le Fluidized Bed Reactor pour purifier le polysilicium
La purification du polysilicium par méthode FBR (Fluidized Bed Reactor) qui utilise beaucoup moins d’énergie que la méthode standard permet aussi de réaliser un gain carbone considérable (jusqu’à -50%). Bien que moins coûteuse, cette méthode est encore très peu utilisée. À surveiller donc…
On peut citer aussi l’augmentation constante de la taille des lingots, la diminution de l’épaisseur des wafers, la diminution de la quantité d’argent pour la sérigraphie des contacts des cellules… Plus généralement, une politique interne de consommation optimisée de la matière première et de réduction des pertes aura un effet positif. Il en va de même pour l’ancienneté du parc machines, généralement les nouveaux outils de fabrication consomment moins, on priorise donc ces lignes pour les ACV.
Quelles sont les cibles prioritaires d'optimisation ?
L’expérience accumulée dans l’analyse de l’impact carbone de chaque étape de fabrication nous a permis de prioriser des pistes d’optimisation et donc l’investissement dans des ACV. Le graphique ci-dessous qui récapitule les valeurs d’émissions carbone standards (méthode 1) et optimisées (méthode 2) nous permet de faire les constatations suivantes :
- ACV indispensables pour la partie Polysilicium et Wafer
- Fort impact de la partie Lingot monocristallin, ACV à réaliser
- Peu d’intérêt à réaliser des ACV pour la partie cellules et modules
De plus, l’utilisation des process moins carbonés décrits ci-dessus permettront une optimisation encore plus intéressante.
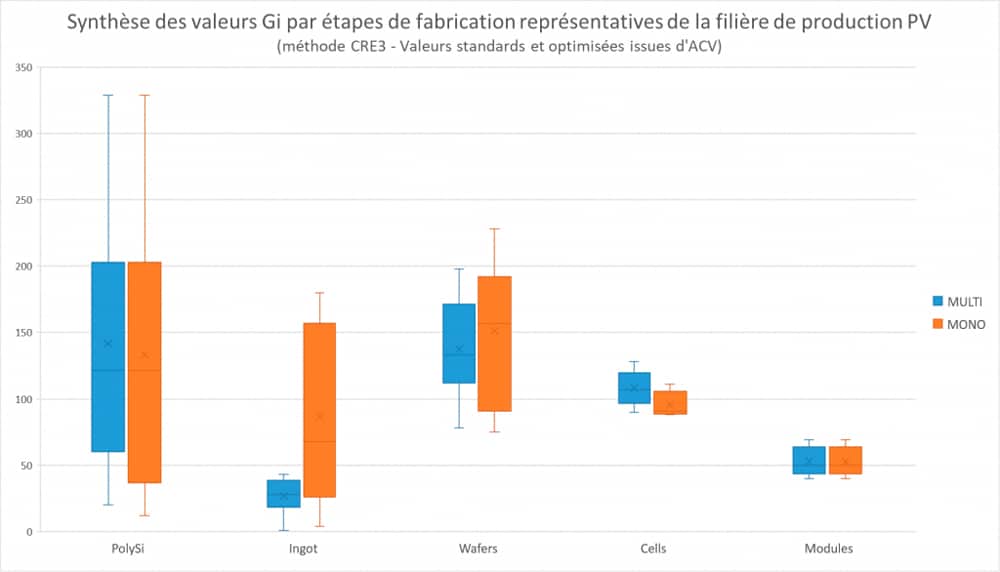
Les valeurs issues du Polysilicium et Lingot norvégiens sont aussi incluses dans ce graphique. Nous aborderons dans le Chapitre 5 les enjeux de ce supply.
*02/2016 ELKEM annonce la production de 5000 tonnes de lingots/an en redémarrant une partie des anciennes usines REC à Herøya. Source : https://www.tu.no/artikler/na-skjer-det-elkem-starter-nytt-soleventyr-pa-heroya/277211